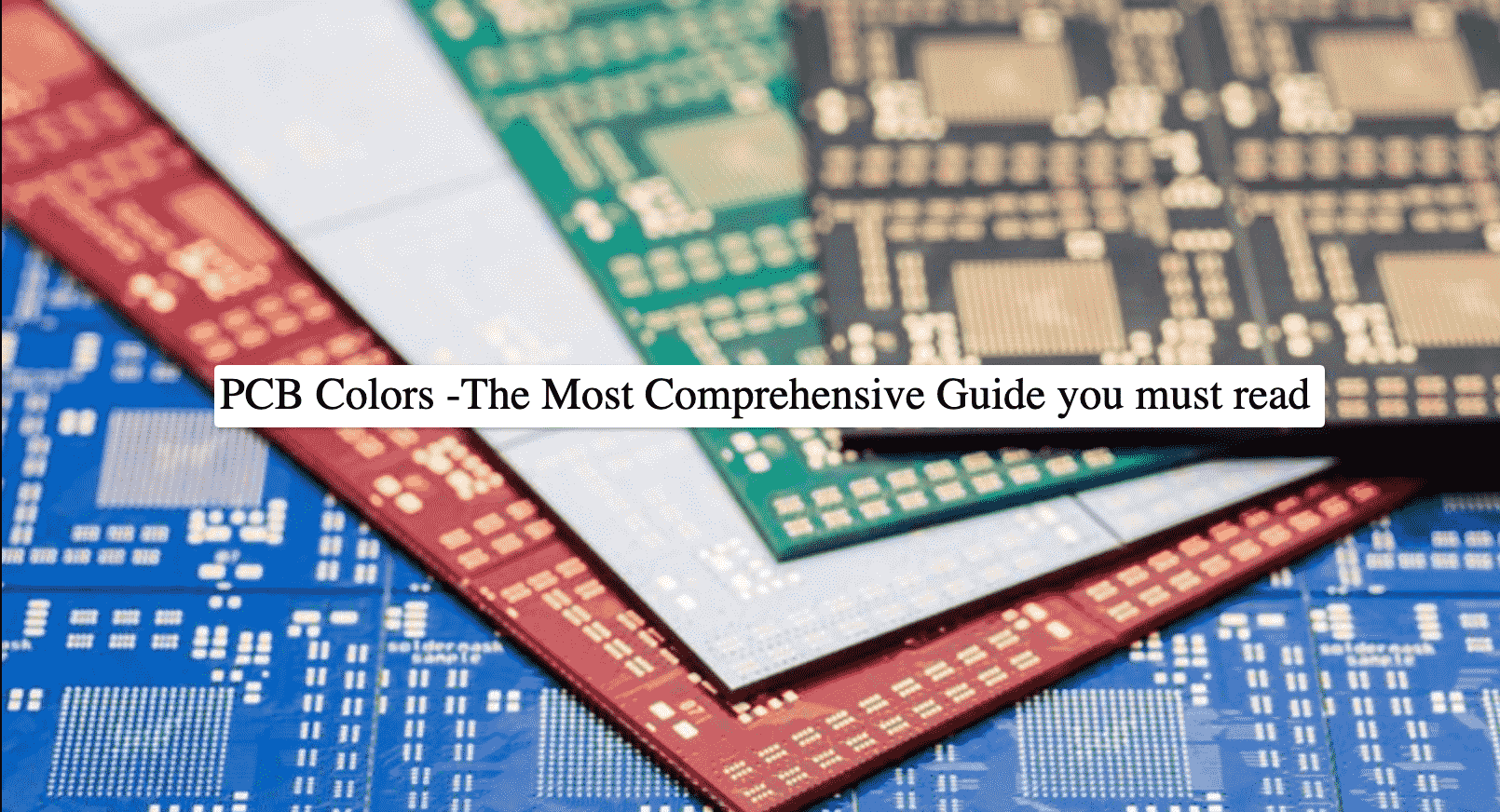
PCB Colors -The Most Comprehensive Guide you must read
Do you ever wonder why there are different colors on your PCB? Or are you uncertain about which PCB color you should go for your circuit board? Well, this article gives you the information on these questions.
We shall also get more information on the likely problems you will face with the PCB colors you may choose. By the time you finish reading the article, you will know the best option to customize, buy, and design the most suitable PCB. With the clear elucidation of all the important factors that decide the value of the PCB colors, you can know for sure which PCB color you can opt for and get the best out of your spending.
What is the PCB Color?
This is but obviously the first question to strike one’s mind after taking a look at the number of color options in PCBs. Knowing what PCB colors are, we must be aware that the pigmentation we see on a PCB isn’t the actual color of the first board. It is a covering applied to the FR-4 PCB material. The color on every board result from the color of the solder mask placed to protect the bare copper wires.
Selecting the solder mask’s or solder oil’s color must have a nice visual disparity to the swathing copper wires, and they become distinguishable. Therefore, applying the color helps the designer and repair technician find the copper wires easily due to the contrast with the color.
The colored layer safeguards the copper wires from getting into short-circuits. It also makes a layer of protection from regular wear and tears to the board caused by use and environmental stress or any other cause of damage to the board.
Type of PCB Colors
PCBs are available in several colors; green being the most common one, blue, yellow, white, clear, black, and purple PCBs, to name a few. What is the main concept behind the PCB colors? Every board’s color choice differs and will usually depend on the designers’ personal preference, not unless the customer has stated specific demands.
Secondly, many designers and PCB or electronics manufacturers use PCBs with colors that are not customarily used for aesthetic purposes. Such PCBs are typically implemented in transparent or translucent electrical devices. Hence, the mere color of the PCB or the combination of the PCB color along with the structure material color can make the electronic look attractive.
Color Classification of Solder Mask
Choosing the color for the circuit board depends on the designers as well as the consumers. Consumers’ usual preferences are taken into accounts while choosing the PCB colors.
- Blue circuit board
Arriving next to the green circuit board in demand and prevalence, the blue circuit board finds its way in many PCBs. The distinction between the shade and the copper wires makes it simple to assemble and repair it.
- Red circuit board
The red circuit board is one of the most striking and aesthetically appealing PCB colors often regarded by many designers worldwide. They also offer an obvious distinction in the traces, planes, and spaces within the board, making it effortless to spot any damages on the board immediately. It is also useful when using magnification when attempting to spot out problems that need magnifying glasses on the board trails.
- Black circuit board
The black circuit board is one of the most intricate circuit boards. With the blackboards, it gets almost improbable to distinguish between empty spaces, planes, and traces. Therefore, you may need to tilt the board for better clarity while casting a beam of light to inspect such problems.
However, on the other hand, working with the pads becomes very well defined. It simplifies the process of identification of the spots but also if correctly marked. Apple as a brand is known for using black PCBs for their boards in the production of iPhones and MacBooks.
Also read:- Guide on PCB gold fingers
- White circuit board
The white circuit board is the poorest selection of your solder mask since it doesn’t display any visible distinction at all. Working on a black PCB is still much easier than working on the white one. Using light at any angle cannot help someone find trails or signs of stress.
Using magnifying glasses is also usually not much help, even for trained eyes. Hence, white circuit boards are usually not seen around as they affect the electronic devices’ reparability.
- Purple circuit board
The purple color isn’t a regular color for manufacturing a PCB. Depending on your company, you may have to pay an additional price for selecting this color. On the purple PCB, the visible contrast is great, and the overall reparability is increased.
- Yellow circuit board
The yellow boards are spectacular to work with, and it is yet a wonder why most engineers do not opt for yellow to mask the solder color. Yellow offers greater detail of visible contrast between traces, empty spaces, and planes. It is similar to the green color mask with efficiency and high reparability.
- Green circuit board
Green is the commonest color of a typical PCB, and it has been so for several years, perhaps for many decades. To know why it has been a favorite color among many designers, we understand why the green color in PCB offers ease in application.
Why are Printed Circuit Boards Usually Green?
While thinking about PCBs, green PCBs are the first and mostly the only thing to pop up in our mind. But why has this been the chosen color over the decades?
- Green can decrease fatigue to the eyesight
The green color isn’t as bright as the pink or red color. Also, when it comes to PCBs, most PCB makers opt for dull green. The color doesn’t affect most designers’ eyes; they can work on the board for more extended hours than those with brighter colors.
- It has physical benefits
The visible contrast levels are another critical thing. The designers and repair technicians get more visible differences in empty traces, spaces, and planes. Hence, talking about examinations and repairing, green color makes it easy to recognize a problem and get it resolved quickly.
- It facilitates mass production
The green color has been around for an eternity, and it is now the general color code for manufacturing PCBs. The resources available to produce them have become easily accessible and widely available to PCB manufacturers that too in large quantities. Since this is the color most companies prefer and use, it promotes mass production.
- Lower price
Due to mass production, the availability becomes easy; therefore, it decreases the prices greatly. Hence, for custom colors in your solder mask, one has to pay the extra cost. The inexpensive prices of the green solder mask make the green PCBs a regular color on most circuit boards.
Read more:- A detailed guide on flexible PCB
How to Choose the Right PCB Colors?
Now, coming to the point on how to select the ultimate color for your PCB board!
- Consider other PCB product combination
Green is one of the easily obtainable colors to use for the solder mask. Generally, this coat is the thinnest; it has a layer of only 0.1 mm thickness. The green color for PCB is also optimum to function well with as many PCB components as possible simplifying it for repairs and assembly on the board.
- Take matte and glossy surfaces into consideration
Opting between a matte and glossy finish is entirely the designer’s choice. Both works perfectly well; with the shiny finish, they become more reflective and appear to have a hard shell-like finish, whereas the matte finish has a porous finish and gives it a darker look.
- Take the Price and batch into considerations
When picking your solder mask color, green will always be at the top of the list. It is quite affordable amongst all the colors and widely obtainable in huge quantities. One can also get a good price from a manufacturer.
The Difference between Different PCB Colors
When talking about the differences between the PCB colors, there’s nothing more outstanding than what effects one color has on the PCB functionality. In the manufacturing unit and repairs department, someone will have difficulty or ease with the visible contrast of the board and the PCB parts. Nevertheless, there are some minor differences.
- Financial matters
When it comes to prices, the green color is very affordable and is a certain choice for most designers and manufacturers. It is a widely accepted color for making PCBs, and it will surely be very cost-effective for your project.
- Practical differences
Besides the assemblage or repair, the workings of the solder mask of all colors are all the same. The main purpose is to give a coating for PCB components.
Aesthetic appeal is one factor some consumers may go for. However, it is only applicable if the devices have a see-through PCB assembly.
- Possible difficulties in the printing process
Regardless of which PCB color you choose a possible situation during the process of printing is the ink stickiness can be high or low, making gluing to the board very poor. You may have to raise or decrease the consistency of the ink. Although this is a prevalent scenario, here are some issues a manufacturer is likely to face.
* Bad squeegee
* High silk screen pressure
* Differences in the distance between the screen and the printing surface
How to Choose the Right PCB Colors Supplier?
Opting for the right circuit board colors supplier means opting for one that is consistent in providing the color and the right quantity. It would help if you had a well-established supplier in the market and possesses a good knowledge of the PCB colors. Understanding that the circuit boards are the main component of any electronic material, you must choose a supplier who can apply the solder mask accurately.
Besides, the manufacturer of the PCB ink has to have a good repute in the market. Some manufacturers have been in the industry for over some decades. Asking for after-sales support is the best way of ensuring that the manufacturer is worth dealing with.
Conclusion
In this article, we have tried to discuss important points about different colors used in the manufacturing of PCBs. PCBs are available in various colors, namely green, blue, white, yellow, red and purple. The green color is the choicest and the most prevalent in the PCB manufacturing process. The article also tried to emphasize the use of the green-colored PCB. Nevertheless, many manufacturers choose colors for aesthetic reasons.
While the choice of different PCB colors differs between the manufacturers. The green color for manufacturing PCBs is the choicest due to its practical advantages like cost-effectiveness, easy availability, and a lot more.