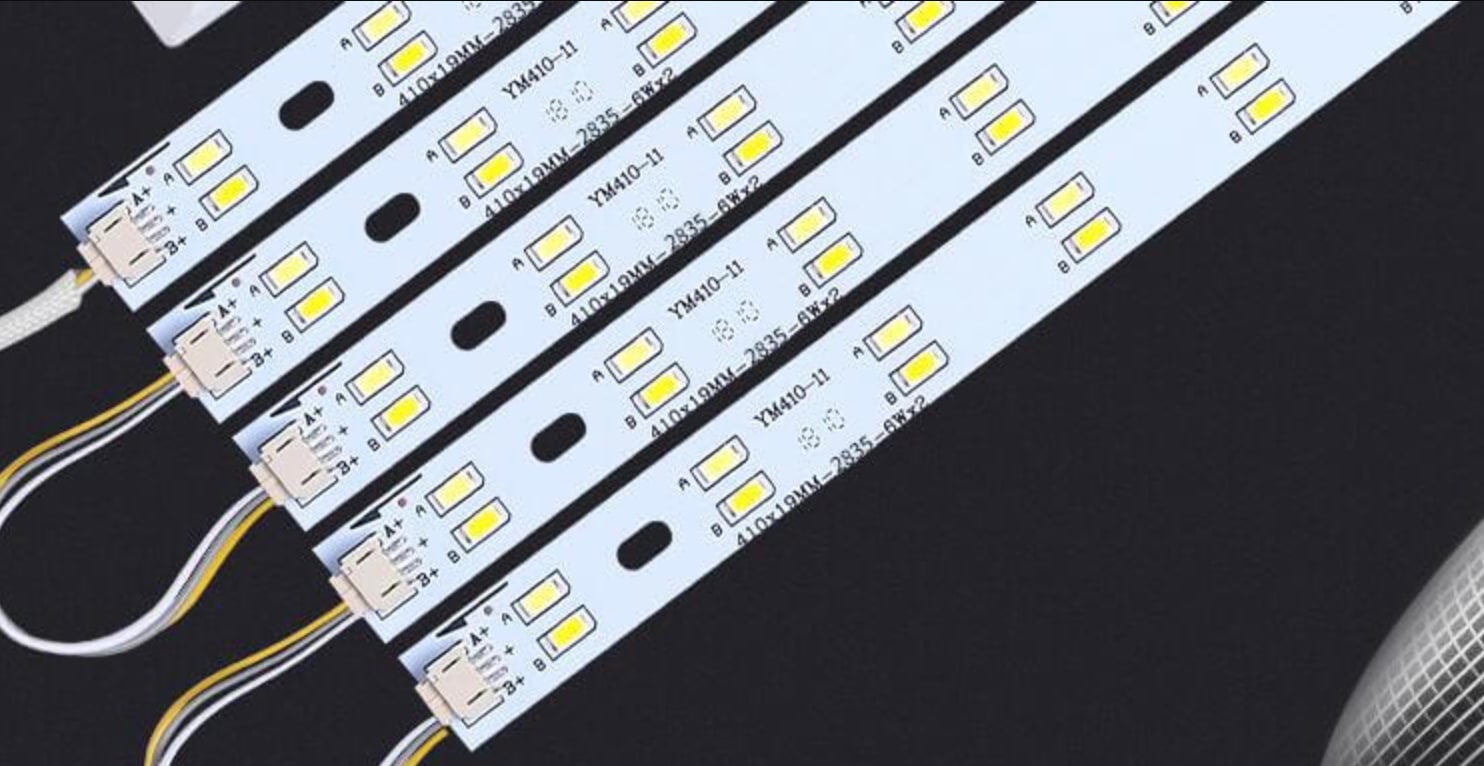
Things to know about flexible LED strip substrates
LED lighting strips, sometimes called LED PCB strips or LED tape, are made from an agile printed circuit board with attached light-emitting diodes (LEDs) organized straight. These light strips give adaptable and energy-effective lighting options by providing illumination for various purposes. LED PCB strips are available in various measurements, shades, and intensities for ambient lighting, ornamentation, signage, or everyday use. Because of their effectiveness, resilience, and simplicity of setup, they are well-liked for commercial and residential applications. Their adaptability enables them to adjust to many forms and materials.
Materials Used to Make PCB LED Strip
The LED PCB strips consist of various parts, and each of them is made using varied materials. The following are the parts of the strips and the materials used to make each component.
LEDs constitute the strips’ parts that generate light, resulting in illumination. Electrical current that travels across semiconductor components, or LEDs, causes it to release light. They come in different hues and intensities of brightness.
Printed Circuit Boards: For mounting the LEDs, printed circuit boards (PCB) function as PCB substrates or foundations. It supports the LEDs’ power connections as well as mechanical stability. PCBs are made of a variety of materials.
Base Materials: The following are the most popular base materials:
- FR-4: A prevalent material for the substrate consisting of an epoxy-based binding agent and woven fiberglass fabric. In addition to tensile strength, it has electrical solid insulating qualities, making it ideal.
- Aluminum: Due to their metallic core, aluminum-based printed circuit boards are suited for LEDs with considerable power and aid in dissipating heat.
- Flexible circuit boards: Flexible circuit boards are utilized in flexible LED strips. They can be bent and adjusted for purposes that call for flexibility, including surfaces that are curving or small places. They are composed of malleable substances like polyimide.
- Copper Trace Elements: These conducting trails connect the LEDs and different parts to the PCB. Since copper has high conductivity, it is the principal material for these elements.
- Solder Cover: A solder cover or mask is placed on the PCB to shield the copper lines and guard against electrical shorts. The copper is usually covered in a colorful substance, except where electrical cables are established.
- Covering or Encapsulation: To keep the different parts safe from physical harm, humidity, and dirt, several LED strips feature a case or waterproof covering. Materials like silicone or epoxy may be employed to create this covering.
- Connectors and Cables: These components make it easier for a PCB LED strip to be attached to different strips or electrical outlets across longer distances. Usually, they are composed of alloys, copper, or similar conductive substances.
LED Strip Thickness Parameters
The kind of substrates employed determines the LED strip thickness when it comes to a flexible LED strip. Their layout influences the general thickness of flexible LED strips, usually based on thin, pliable platforms like flexible PCBs.
Flexible Substrates: Due to their flexibility, LED PCB strips manufactured on bendable substrates—frequently composed of polyester or polyimide—tend to be thinner. These backings allow the LED panels to flex or adapt to curves, making them ideal for installations in confined areas or other uses needing mobility. According to the layout and materials, the flexible LED strip may have thicknesses ranging from 0.5mm to 2mm.
LED Chip Setting: Packaging the LED chips also affects the thickness of the LED PCB strips. Though tiny in size, the LED chips might vary in thickness depending on how they are packaged, what is used for bonding, and how the LED strip is designed. Compressed LEDs and developments of chip-on-board (COB) technologies allow smaller LED packages, which contribute to more minor LED strip pcb features.
Steps in Designing LED PCB Strips
There are various steps involved in the process of designing the LED strips. Depending upon the intended use of the led strips, the designing stages and parameters might vary slightly. However, the basic steps remain the same. The following are the steps involved.
- Recognize the Requirements: Establish the needed dimensions, brightness, hue, and voltages for the LED PCB strips, among other characteristics. To customize the layout, ascertain the intended use and location for the strips.
- Pick The Components: Using the foundation of the desired variables, select high-quality LED chips, suitable resistors, and other electrical components. Consider variables, including current and voltage rankings and thermal regulation, to ensure effective functioning.
- PCB LED Substrates: Choose the PCB substrate materials considering the planned use. FR-4, aluminum, and polyimide are stiff and flexible substrates that can be used based on the setting context, mobility demands, and design criteria.
- Trace Alignment: Consider the voltage loss and current-carrying capability while determining the copper traces’ dimension and placement. Reducing resistance and heat accumulation is made easier with a sufficient trace size.
- Circuits Layout:
-
- Build a circuit schematic by utilizing LED PCB strip design tools and software.
- Place the LEDs onto the PCB according to their orientation.
- When designing the traces, consider the power source and voltage loss across the strip, ensuring the LEDs are connected sequentially.
- Element Orientation: Precisely place the resistors, LED chips, and other parts on the board’s layout. To aid in soldering and prevent electrical disruption, ensure the orientation and distance are correct.
- Heat-Related Factors: Incorporate heat-relieving padding or channels to disperse the heat produced by the LEDs. Thermal overload can impair the efficiency and longevity of LEDs; proper thermal control avoids this.
Testing and Prototyping:
- Make a model of the planned LED PCB strips.
- By performing extensive testing, check electrical characteristics, luminosity, color precision, and functioning.
- If needed, make the relevant modifications before sending it for mass production.
Applications of LED PCB Strips
As mentioned earlier, the LED strips can be utilized for various applications. Depending upon their intended use, they can be produced variably to meet the desired needs. The most common usages or applications of these strips include the following:
- Ornamental Lighting: In residences, cafes, hotels, or stores, such strips are often used as decorative lighting. They provide imaginative lighting options for areas around furnishings and beneath cupboards, which improves ambiance and beauty.
- Stage Lighting: A flexible LED strip is a popular choice for theatrical backgrounds, ambient lighting, and special effects in cinemas, concerts, and other activities because of its flexibility and variety.
- Architectural Lighting: LED PCB strips create attractive designs, emphasize specific locations, or outline building structural aspects. They additionally serve for decorative lighting.
- Retail Displays and Signs: LED lights are utilized in digital screens, lighted signage, and retail signage because they provide vibrant and captivating images.
LED strips are commonly used as lighting sources for various purposes. Their diversity is what makes them special. This diversity also makes it vital to design their PCBs appropriately by selecting the right materials and following the correct procedures. Once accomplished, these can transform any place into a more attractive one.