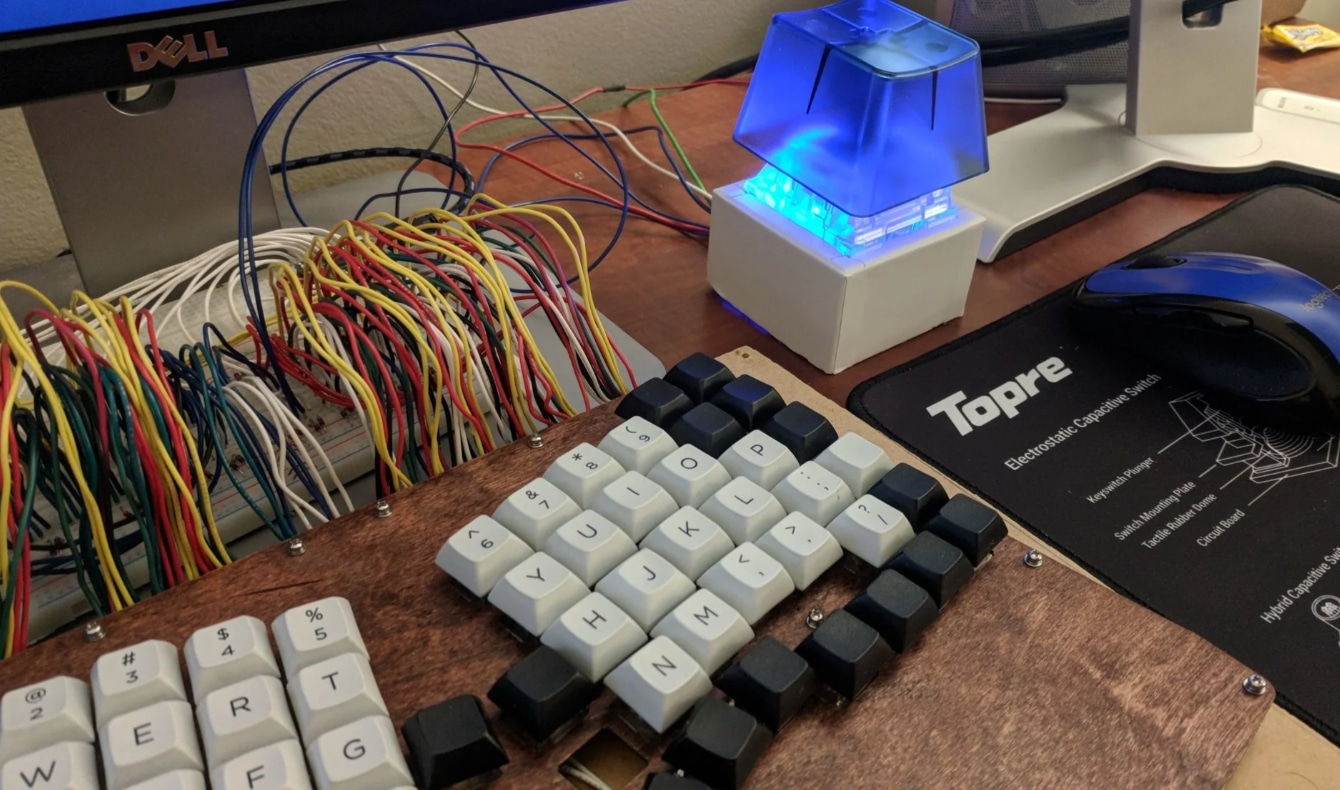
What is Big Switch PCB ?
Big Switch PCB
A big switch PCB is essential for equipment or devices that require high voltage and power to function appropriately. This type of PCB is created and manufactured to handle high power flow. It is a critical element in regulating and controlling this flow to ensure the safety of the equipment and the users. With the help of big switch PCBs, manufacturers of various devices and equipment can get better capability to control high currents or voltages within the equipment. This is achievable through carefully designing high-power components created through precise layout methodologies.
Application Cases for Big Switch PCBs
A big switch PCB can be utilized for various applications wherein the regulation, control, and flow of high voltages through the printed circuit board are needed. Some of the leading equipment where these PCBs find usage include inverters, alternating current motors, chargers for batteries (particularly vehicular chargers for electric vehicles), HD and fluorescent lamps, as well as switch mode power equipment that is used for regulating direct current outputs from alternating current sources.
While these are the primary use cases for big switch PCBs, they also find application in UPS equipment, welding equipment, and other power electronic systems that need to handle high voltage flows.
When selecting the specifics of the big switch PCB for different applications, it is essential to consider the performance requirements for the equipment. Different equipment has different needs, and choosing the right PCB size to match those needs is critical. Generally, a bigger big switch PCB is better suited for heavier applications. The more vividly spaced components on the larger surface enable better performance and facilitate more efficient heat dissipation.
However, only the PCB size can be determined depending upon the equipment size. As such, the manufacturer must integrate features like heat dissipation channels when the equipment size is relatively small.
Designing Considerations for Big Switch PCBs
When designing this type of printed circuit board, the big switch PCB manufacturer must consider several factors. From layout designing to choosing suitable materials, deciding on the voltage capacity it can handle, integrating safety circuits, and more, there are multiple factors to ponder. The main elements that need to be planned for effective big switch PCB manufacturing include the following:
Material Selection: The first step in designing and manufacturing a big switch PCB is selecting the proper base materials. The big switch PCB manufacturer ought to consider the best choice based on application requirements, from insulated metal substrates to other conductive options. An essential factor to check is the ability of the materials to stand at high temperatures.
Designing the layout: Before the PCB can be sent for manufacturing, it is critical to set and inspect its potential layout. While designing the layout, certain important checkpoints to look for include:
1) Spacing between the various components, particularly high-voltage elements
2) Room for heat elimination or creation of channels that allow dissipation of heat
3) Isolation of high-voltage components from other components
4) Properly soldered joints
By paying attention to these aspects during the designing phase, creating a successfully performing PCB that reflects only some significant issues is possible.
Deciding Layer Counts: When designing the big switch PCBs, the circuit board can have multiple layers depending on usage and application. Typically, a big switch PCB supplier or manufacturer must choose between six to twelve layers of copper to successfully build a board with dimensions up to 600mm x 600 mm. During the designing and planning of the layers, they would also have to determine the thickness of each copper layer, which generally ranges around 2oz.
Incorporating Safety Features: During the designing of the big switch PCBs, the circuit board must be integrated with a set of safety mechanisms, including fuses, thermal shutoff mechanisms, voltage monitoring systems, snubber circuits, as well as suppressor mechanisms. Each of these safety measures offers a distinctive benefit. For instance, The thermal shutoff system prevents the circuit board from overheating. Similarly, as the name suggests, the suppressor mechanism provides greater control to limit spikes in voltage or current. These safety elements are critical for the big switch PCB to function properly.
Testing and Inspections: While manufacturing the big switch PCBs, a good practice is to develop a prototype or inspection unit, check it for its functionality and performance, and only upon complete satisfaction, send it for bulk manufacturing. This helps eliminate the risk of bulk error and wastage of the equipment or part, saving costs and time.
Advantages of Using a Big Switch PCB
Big switch PCBs offer many advantages, such as saving expenditures, improving reliability, enhancing safety, and promoting productivity despite being considerably smaller.
- Security of Use: When manufactured correctly, a big switch PCB offers greater safety for applications that require higher power circulation. Due to their capability to control current flow and voltage regulation, the circuit board makes it safer for end users to use the machines worry-free.
- Saving Costs: A big switch PCB saves manufacturers and end users significant expenses by being high quality and caliber. The high reliability of the circuit board makes them more beneficial for manufacturers who can easily and quickly manufacture more pieces. Additionally, by not breaking down frequently, they save costs for end users who can use the equipment for a long time.
As is evident, big switch PCBs offer a lot of reliability and safety for using heavy power-requiring equipment. With their applications extending to everyday use products, these are a major part of electronic equipment manufacturing. By thorough designing and careful inspections, it is easy to develop high-quality big switch-printed circuit boards that extend the longevity of the equipment within which they are integrated and improve the machine’s overall performance.