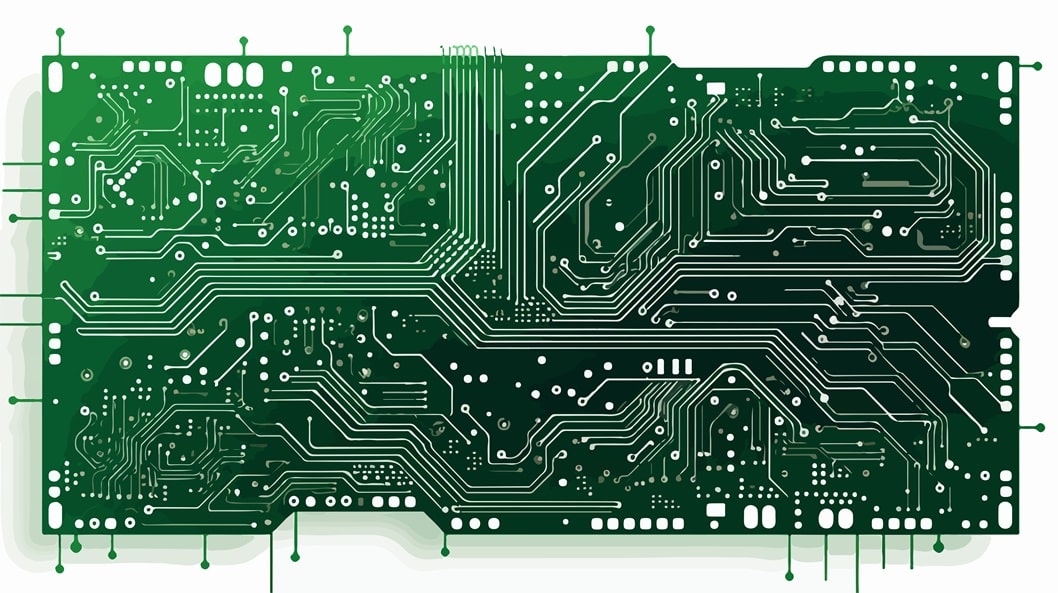
Everything you need to know about Printed Circuit Board Assembly
Printed circuit boards (PCBs) are the backbone of nearly all modern electronics, from smartphones to medical devices. As the global PCB market continues to expand, projected to reach $75 billion by 2026, understanding the intricacies of PCB assembly becomes increasingly important.
Printed Circuit Board assembly is a complex process that involves connecting electronic components to a circuit board to create functional devices. This article provides a comprehensive overview of PCB assembly, including the different types, technologies, and benefits associated with it.
What is Circuit Board Assembly?
PCB assembly is the process of connecting electronic components to a printed circuit board, creating a functional electronic circuit. This process can vary depending on the type of components used and the design of the PCB.
- Assembly with Through-Hole Components: In this method, components have leads that pass through holes in the PCB. These leads are soldered on the opposite side of the board. This technique is ideal for components that need to withstand mechanical stress, such as connectors and switches.
- Assembly with Surface Mount Components: Surface mount technology (SMT) involves placing components directly onto the surface of the PCB. SMT allows for more compact and higher-density assemblies, making it a popular choice for modern electronic devices.
- Assembly with Mixed Components: This approach combines both through-hole and surface mount components on the same board. It takes advantage of the strengths of each method, offering flexibility in design and component placement.
- Assembly on Single Side of Boards: In single-side PCB assembly, components are mounted on only one side of the board. This is a cost-effective solution for simpler circuits and is often used in consumer electronics.
- Assembly on Both Sides of Boards: Double-sided PCB assembly allows components to be mounted on both sides of the board, increasing the available space for circuit design. This method is used in more complex circuits requiring higher component density.
Understanding PCB Assembly Process
The Printed Circuit Board assembly process is a crucial step in the manufacturing of electronic devices, involving the installation of electronic components onto a printed circuit board (PCB) to create a complete and functional circuit. This process can be broken down into several key stages:
- Preparation: Before assembly begins, the PCB is prepared by applying a solder mask and silkscreen layer. These layers protect the board and ensure accurate component placement.
- Component Placement: Components are placed onto the PCB based on the circuit design. This can be done manually for small batches or automatically using pick-and-place machines for high-volume production.
- Soldering: The placement of components is followed by soldering to establish electrical connections. This can be done through various methods:
- Wave Soldering: For through-hole components, the PCB is passed over a wave of molten solder, which makes contact with the component leads and forms solder joints.
- Reflow Soldering: For surface mount components, solder paste is melted in a reflow oven to create solder joints.
- Inspection and Testing: After soldering, the assembled PCB undergoes inspection and testing to ensure all connections are solid and the board functions as intended. This can include visual inspection, automated optical inspection (AOI), and functional testing.
- Final Touches: Any necessary adjustments, such as removing excess solder or correcting defects, are made before the final product is packaged and prepared for shipment.
PCB Assembly Process Technology
PCB assembly involves several key technologies that ensure the efficient and accurate placement of components.
Auto-Insertion: This automated process inserts components into the PCB holes, which are then soldered. It’s particularly useful for through-hole components and enhances assembly speed and accuracy.
Wave Soldering: Wave soldering involves passing the PCB over a wave of molten solder, which flows through the component leads and creates solder joints. This technique is efficient for high-volume production.
Glue-Dosing: Adhesive glue is applied to secure components before soldering. This method helps stabilise components during assembly and is often used in conjunction with SMT.
Solder-Paste Deposition: Solder paste is applied to the PCB using a stencil, which is then reflowed to create solder joints. This process is critical for surface mount assemblies and ensures proper component placement and soldering.
Pick-n-Place: Automated machines pick up components from reels or trays and place them onto the PCB. This technology is essential for high-speed and precise assembly, especially for SMT.
Reflow Soldering: In reflow soldering, solder paste is melted using a heated oven, forming solder joints between the PCB and the components. This method is commonly used for SMT and ensures strong and reliable connections.
Benefits of PCB Assembly
High Precision and Accuracy: Advanced assembly techniques, such as automated pick-and-place machines and reflow soldering, ensure precise component placement and soldering. This precision is crucial for maintaining signal integrity and minimising errors in complex circuits.
Enhanced Electrical Performance: Proper PCB assembly reduces electrical noise and interference, improving the overall performance of electronic devices. Techniques like controlled impedance routing and proper grounding contribute to better signal quality and reliability.
Miniaturisation: Surface mount technology (SMT) allows for the placement of smaller components and higher component densities on the PCB. This miniaturisation is essential for designing compact devices with advanced functionalities.
Thermal Management: Effective PCB assembly practices include the use of thermal vias and heat sinks to manage heat dissipation. Proper thermal management prevents overheating of components and ensures stable operation of the electronic device.
Robust Mechanical Stability: Through-hole components and specific assembly techniques provide enhanced mechanical stability for components subjected to physical stress. This robustness is vital for devices that experience frequent handling or environmental conditions.
Automated Quality Assurance: Automated optical inspection (AOI) and X-ray inspection technologies are used to detect soldering defects, misalignments, and other issues in the assembly process. These quality control measures ensure high reliability and reduce the likelihood of defects in the final product.
Conclusion
Understanding Printed Circuit Board assembly is essential for anyone involved in electronics, from design engineers to manufacturers. The various assembly techniques and technologies not only enhance the functionality and reliability of electronic devices but also offer significant benefits in terms of cost efficiency, performance, and design flexibility.
If you’re looking for expert support and top-notch PCB assembly services, don’t wait and get ready for partnering with Absolute PCB Assembly. Our advanced capabilities and commitment to quality ensure that your projects meet the highest standards and are delivered on time.
Reach out to our experts today to learn more about how we can help bring your electronic designs to life.