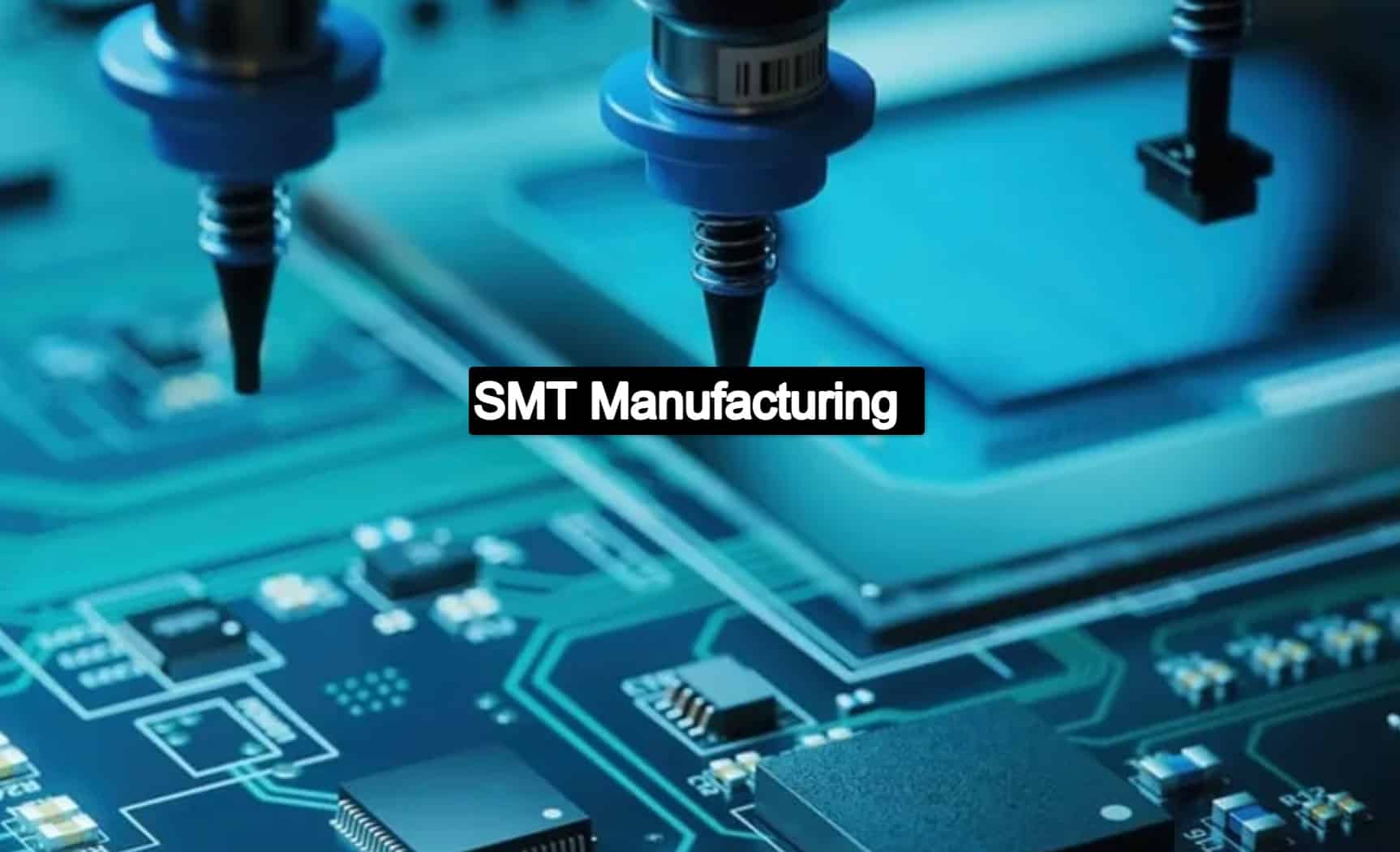
SMT Manufacturing – Advantages and Disadvantages
The technique of assembling electrical components upon a printed circuit board is known as surface mount technology manufacturing, or SMT production, within the electronics sector. Unlike traditional techniques employed through hole innovation, SMT mounts electronic elements right upon a PCB’s substrate. With this technique, parts are placed and soldered upon the top layer of the board by computerized equipment, enabling the creation of electronic boards that are more compact, lighter, and more tightly packed. SMT fabrication is an essential step in electronics manufacturing.
Surface Mount Technology Advantages and Disadvantages
Advantages
- Size Reduction: Electrical more lightweight, sleeker, and diminutive electrical devices can be made more efficiently and perfectly through SMT manufacturing. Space-saving layouts are produced by utilizing smaller parts that may be arranged more closely to each other on the circuit boards.
- Increasing Components Volume: Surface mount technology may increase PCB element densities. Electrical devices can perform better in general because of this increasing concentration, which enables more excellent capability in a more compact size
- Enhanced Electrical Operation: Smaller connector routes in SMT structures improve gadget functioning by reducing interference with signals and improving electrical effectiveness.
- Economic Efficacy: The SMT process saves expenses due to the automated production methods. Labor expenses are decreased, and manufacturing productivity is increased by robotic soldering and element positioning.
- Increased Swiftness and Effectiveness: Assembling SMTs is quicker than assembling them through holes. Automated machines can swiftly and concurrently insert several parts, which accelerates.
- Adjustment to Cutting-Edge Technology: Because SMT machines can handle integrated circuits and smaller-sized elements, they can accept cutting-edge technological developments and improvements in electronic parts.
- Diminished Weight and Materials Consumption: Systems with tinier electronic parts and reduced printed circuit boards are less heavy, offering benefits for consumer gadgets and aviation sectors. It also uses less material, contributing to a more ecologically responsible production process.
Disadvantages
- Part Dimensions and Manufacture: Holding and managing microscopic SMT elements throughout assembling might be more complicated. This may raise the possibility of damaged parts or misplacing.
- Need for Specific Machinery: Specific equipment, including pick-and-place equipment or reflow-type ovens, is needed for the surface mount process. These devices have a potentially significant initial expenditure requirement.
- Difficulties in Reworks and Repairs: Because SMT systems include surface mount elements and tinier, more elusive size requirements than through-hole elements, changing or fixing them might be more challenging.
- Issues With Durability: Many contend that SMT machine soldered junctions could not possess the same structural robustness as through-hole soldered connections, which could result in dependability issues when subjected to harsh environments or mechanical strain.
- Increasing Needs for Accuracy: Particular situations may find it challenging to achieve the accuracy required for the SMT process because it relies on increased development and production techniques for precise soldering and element positioning.
SMT Manufacturing Process
SMT plays a critical role in producing modern-day electronics such as laptops, mobile phones, healthcare equipment, automotive equipment, and other gadgets since it allows for greater productivity, accuracy, and the creation of tiny electrical components. Given its vital importance inappropriately constructing electronic goods, the SMT manufacturing processes must be accurately understood and conducted to prevent errors. The following are the steps involved:
- Planning and Organization: Applying specialist software, the arrangement of the PCB is designed to start with the surface mount manufacturing procedure. The structure of the circuit is taken into consideration when choosing supplies. Components like fiberglass-reinforced epoxy composite create the PCB, followed by a soldering overlay applied on top.
- Applying Soldering Compound and Stenciling: A solid steel stencil is positioned above the printed circuit board following the SMT process. Next, The PCB is covered with soldering paste, a combination of flux and microscopic solder fragments, using the stencil. This tool aids in accurately applying the paste to designated regions where parts must be installed.
- Unit Arrangement: Surface mount parts, such as capacitors, resistors, and other similar small elements, are precisely positioned and placed upon the printed circuit board using robotic picking and placing tools. To guarantee proper installation, such devices’ imaging systems match elements according to predefined printed circuit board locations.
- Reflow Fitting: A reflow-type heater is used in SMT manufacturing to process the printed circuit board after all the parts are assembled. The circuit board is heated inside the oven, which melts the soldering paste and creates a robust and long-lasting connection between the circuit board and its parts. Reflowing solder makes strong electrical links without requiring extra cables.
- Testing: Examination of the PCB occurs after the reflow procedure is completed. X-ray equipment and automatic optical inspection technologies look for element misalignment, soldering flaws, and other assembly-related problems. This procedure guarantees the reliability and caliber of the constructed printed circuit boards.
- Subsidiary Mechanisms: It is possible that specific circuit boards need extra steps after construction in SMT production. This might involve testing processes to ensure functioning and implementing uniform coating to shield the circuit board against humidity and other influences.
- Final Examination and Quality Assurance: Comprehensive evaluation is performed on the built printed circuit boards to guarantee that they operate and meet standards during manufacturing. Functionality testing, in-circuit assessments, and additional quality assurance methods are utilized before the item’s final assembly to detect and address any mistakes.
Precautions to Take
- Storing and Managing: You should keep surface mount elements in regulated settings to avoid absorbing moisture and impairment. Employ proper handling equipment to prevent physical damage or electrostatic discharge (ESD).
- Cleaning Up Stencils: Keep your stencil spotless to ensure accurate soldering paste deployment. Maintain stencil cleanliness to avoid inaccuracy or solder pooling when applying the paste.
- Precision of Element Positioning: Ensure SMT parts are placed precisely to prevent electronics manufacturing flaws. Use appropriate machine calibrating and imaging system parameters to accomplish the exact component placement onto the PCB.
- Training of Operators: Give personnel thorough instruction in surface mount technology, particularly in secure handling, machine operating, and following preventive measures. The possibility of mistakes and flaws throughout assembling is decreased by staff who have received proper training.
- Benchmarking Reflow Ovens: Profile your reflowing oven continuously for dependable and uniform solder paste reflow. By monitoring thermal characteristics, you may avoid solder connection flaws caused by either becoming too hot or not enough.
- Quality Assurance Precautions: Ensure everything is up to par during the production procedure. To identify flaws and ensure the structure is intact, use X-ray and automated optical examination equipment.
Manufacturing SMT is critical in ensuring optimal production of printed circuit boards and electronics, of which these components form the backbone. As a complex procedure, it is equally essential to guarantee that trained professionals execute the process to avoid errors and failures in the completed product. In addition to having experts supervise the process, having the exact machinery required to conduct the process in prime condition is vital. By following these methods, it is possible to complete SMT manufacture accurately.