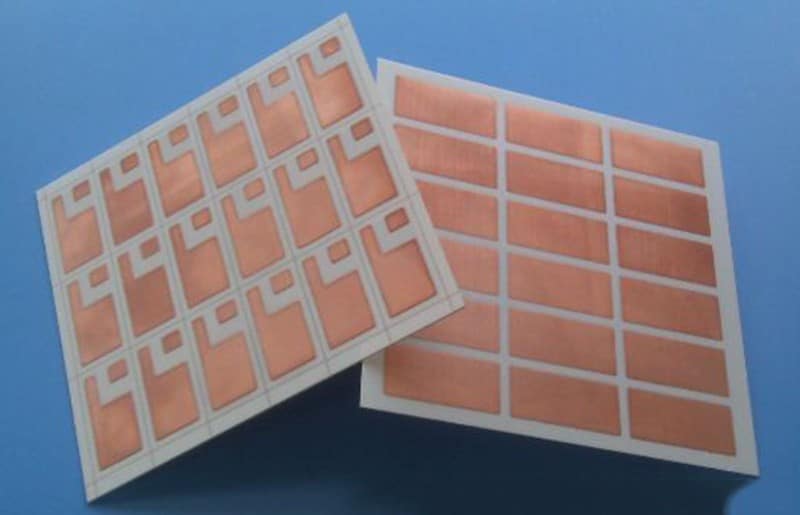
What Is Alumina Substrate?
Ever since the development of PCBs, several variants have raised the requirement for new materials. It is now highly essential to utilize appropriate and best components for the PCB materials, especially the substrates. These substrates help to enhance and construct the PCB accordingly. The alumina substrate is among the most preferred choices among all the substrates used.
What Is Alumina Substrate?
Alumina is among the many different substrates that are used in the PCB production. Many people also know it as the ceramic substrate, which is why it is called the Alumina ceramic substrate. It is one of the most utilized PCB materials due to its amazing breaking strength, better heat and insulating properties, and thermal conductivity. Also, another reason why alumina is preferred across the manufacturing firms of PCBs is that it provides good chemical and mechanical resistance.
What Are The Properties Of Alumina Substrate?
The alumina substrate properties cut the fundamental requirements for producing reliable PCBs. These consist of thermal conductivity as well as heat insulation. The following section highlights the essential alumina material:
- Better Thermal Conductivity
The heat conductive ability is also among the major factors to consider when choosing a substrate for the PCB. When it comes to this, the alumina ceramic substrate is the best choice as it has an enhanced thermal conductivity that helps with heat dissipation in electronic devices.
- Remarkable Mechanical Strength
The mechanical strength is based on the ability of the substrate to add up to the durability and provide resistance to shocks, vibration, and mechanical stress. One of the major reasons manufacturers prefer alumina substrate is its excellent mechanical strength.
- Smoothness
Alumina ceramic substrate provides a combination of less porosity and good smoothness. It is a feature that provides amazing adhesion with both thin and thick film material.
- Better Electric Insulation
A good substrate has heat dissipation, so it must insulate the devices. Similarly, the efficient electrical insulating properties isolate or create the division between the PCB elements.
- Stable Breaking Strength
Alumina ceramic substrate provides remarkable breaking strength and less variance in the shapes and dimensions. The following are the properties of the alumina substrates:
- Corrosion resistance.
- Small dielectric loss.
- Excellent fire resistance properties.
- Smooth surface.,
- Low adherence.
- Small warpage.
- Remarkable dimensional stability in the highest temperatures.
- Chemical properties.
- Stable physical properties.
- Resistance to corrosion and wear.
- Resistance to chemical and oil products.
- Less variance in plate thickness and slit pitch.
Different Alumina Substrates Types
Two primary types of alumina ceramic substrates are used for PCB manufacturing. These two types are Sintered Porous Alumina and Sintered High-Density Alumina.
Before diving into the distinctions and types of alumina substrates, let us explore the primary Alumina substrate compositions:
- Sintered High-Density Alumina
This alumina ceramic substrate consists of an alumina content between 96% and 99.6% and has substrate available in the two products.
For this type, there are varying densities, such as:
- 2mm.
- 1.27-1.52mm
- 0.75-1mm
- 0.38-0.5mm
- 0.15 to 0.25mm
Feature:
- Can be used as electrical insulators.
- Remarkable flatness.
- Low adherence.
- Good thermal conduction.
- Corrosion resistance and
- Abrasion resistance.
- Sintered Porous Alumina Substrate
It is another alumina substrate type and is lighter than the first version. However, it has similar features and properties in regards to mechanical, chemical, and electrical.
Sintered porous alumina substrate is available in the following thicknesses:
- 2mm.
- 1.5mm.
- 1mm.
It supports the following:
- Filtration of gases and liquids.
- Homogenous fluid diffusion.
What Are The Benefits Of Alumina Substrate?
You can get several benefits by using an alumina ceramic substrate for your PCB. Enhancing heat makes electronic products more heat resistant, but you can get many other benefits. We have listed down some of the primary benefits of utilizing alumina substrate for your PCB:
- Efficient Thermal Management
Heat or thermal energy can be the militating factor in regards to the functionality of the electronic device. For instance, when some electrical devices are used, they generate a vast amount of heat. With this, the heat builds up and exceeds the limited temperature, which can damage the device.
Hence, thermal management with alumina substrate is about 30 W/m.K, which allows the substrate to get rid of heat from the electronic devices.
- Extended Lifespan
The alumina substrate’s heat conductivity is beneficial for extending the electronic application’s lifespan. Decreasing the heat within the devices enhances the lifespan of the product being used.
- Efficient Performance
Alumina Ceramic substrates are good electrical insulators that provide reliable performance. The substrate’s durability is why this material is preferred for applications requiring stability.
- High-Temperature Resistance
With higher temperature resistance, an alumina substrate is an ideal option for electronic devices that integrate in places with higher temperatures. Moreover, it makes alumina ideal for locations that need robust performance.
What Are The Applications Of Alumina Substrates?
You can use Alumina PCB manufacturing that needs optimum reliability and performance. You can use alumina substrate for applications like:
- LED Devices
Alumina materials can be used for LEDs as they improve the heat conduction and reliability of the applications. Besides that, these substrates are an efficient option for faster heat dissipation and excessive thermal energy made by LEDs. It leads to better performance and lifespan.
- PCBs
One of the major uses of this substrate is for Alumina PCB manufacturing. The uses of alumina substrate can range from reliability and stability to electronic components and provisions of reliable platforms for making complicated PCBs and installing electronic components.
- Power Electronical Devices
The alumina substrate is also used for power-related electronic devices, such as:
- Power modules.
- Inverters.
These materials are helpful due to their best thermal conductivity properties and electric insulation. Other than these three, this substrate is also used for:
- Chip resistors.
- Liquid filtrations.
- Sintering equipment.
- Medical devices.
- Electronic sensors.
- Overn construction elements.
- Catalyser.
- FAX substrates for thermal printer heads.
Stages Of Alumina Substrate Manufacturing
There are varying steps for the production of alumina substrate, such as:
- Choosing Raw Materials
The raw materials are selected first, and the primary focus is on the distribution of the size as well as the purity of the powder. Opting for top-quality alumina substrate powder allows you to choose the best substrate. Aluminum oxide powder is amongst the most efficient raw material which you can use, as well as aluminum hydroxide. Both can provide the desired composition and consistency, provided the blending and mixing processes are accurately done.
- Preparing Powder
It is easy to create powder with the following steps, such as:
- Filtering.
- Washing.
- Mixing.
- Grinding
- Forming Methods
In this step, the process consists of a powder mixture for making a green sheet. Tape and extrusion castings are some of the primary methods utilized for this purpose. After creating the mixture, the green sheet is cut based on the required shape and size.
- Sintering Process
Sintering is done since the molded alumina substrate does not provide efficient reliance. Hence, it is generally prone to higher-temperature sintering, fusing the particles to enhance the reliability of the product.
After the sintering, you will get a molded substrate with a crystalline structure and dense footprint that consists of the needed mechanical strength with remarkable electrical properties and optimal density.
Conclusion
Alumina ceramic substrate is one of the best materials essential for a wide range of use cases such as LEDs, PCB manufacturing, and power electrical devices with uses across different industries that enhance the lifespan of the products used.