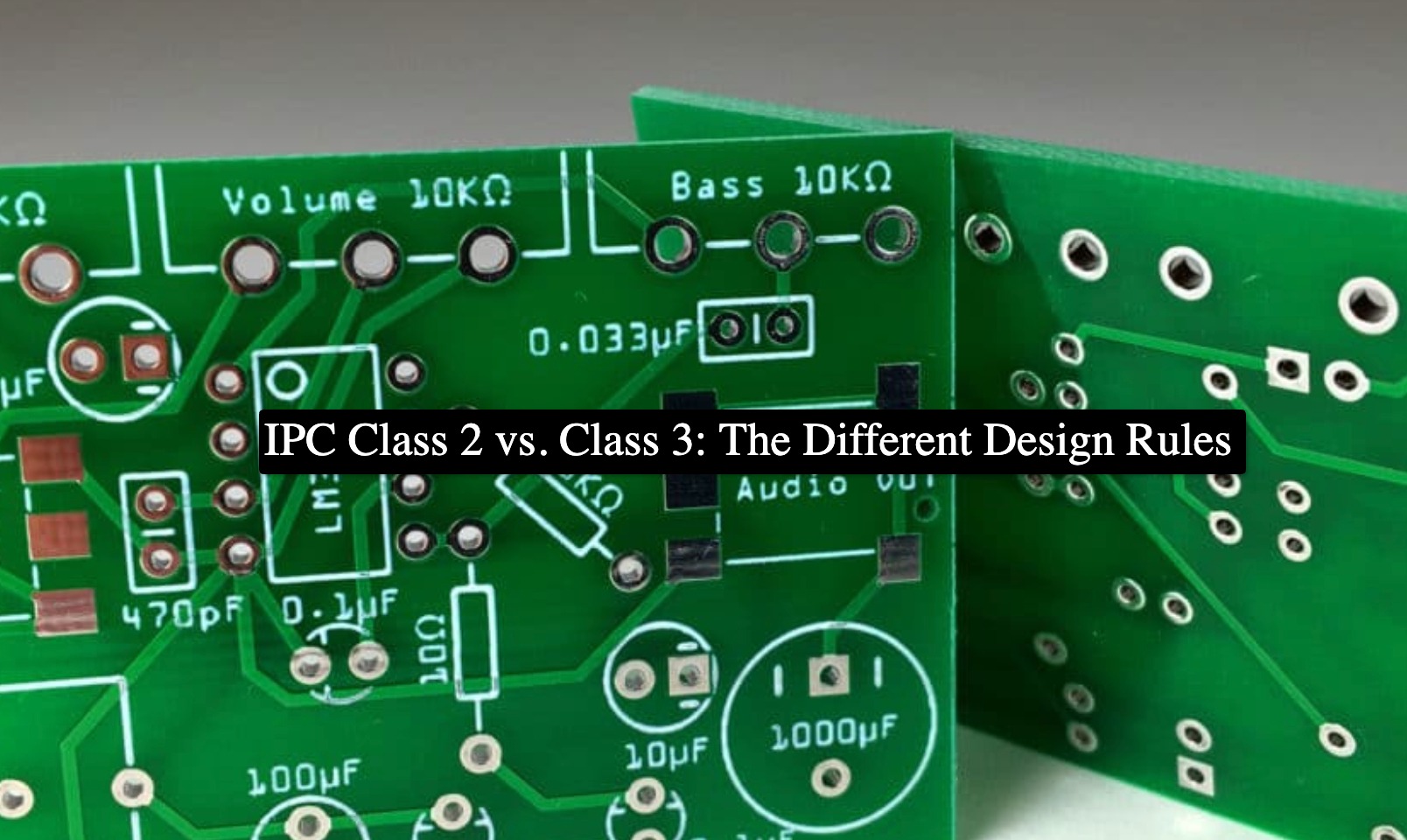
IPC Class 2 vs. Class 3: The Different Design Rules
In 1957, IPC was developed under the Institute of Printed Circuits, now known as the Institute of Interconnecting and Packaging Electronic Circuits. The IPC class aims at standardizing the assembly, the requirements for electronic components, and the production process. This IPC helps in fabricating and designing reliable, safe, and high-quality printed circuit board products.
IPC defines three major types of printed circuit boards. IPC classes for printed circuit boards rely on differing levels of quality for a variety of uses. Each class describes the type of board.
Many new printed circuit board manufacturers require clarification on the various IPC classes. If you are among those who need clarification on IPC class 2 and IPC class 3, you must read this article. It will provide deep knowledge about IPC class 2 vs class 3. By reading this article, we are sure you will understand the difference between each IPC class.
Class 1: General electronic products
The class 1 board has a number of cosmetic flaws that do not impair the functionality of the printed circuit board. It is assigned to general electric products with limited life and simple functions, like toys, LED lights, and more. This class includes the most typical electric products.
The product’s reliability is not crucial on IPC Class 1 boards. They are the cheapest boards to build in the industry but have a limited life expectancy.
Class 2: Electronic product of dedicated services
IPC Class 2 follows a more stringent standard than Class 1, allowing some cosmetic imperfections. These boards are more reliable and have a longer life. This type of board can be found on tablets, smartphones, laptops, and other devices.
Although IPC class 2 is expected to run continuously, this board’s functionality is not crucial. These boards are not exposed to extreme weather conditions.
Class 3: The electrical product that requires high performance
IPC class 3 is the most robust board on the printed circuit board. They can provide uninterrupted services in every weather condition, even in extreme hot or cold. A high level of testing and inspection is conducted on IPC Class 3 boards with strict standards that make them highly reliable. Moreover, there is no downtime with the equipment these boards use.
These boards have set a new benchmark for boards used in military, healthcare, and automotive applications. Apart from the IPC Class 3 standards, these printed circuit boards also meet the additional requirements of IPC 6012E documents.
General difference between IPC class 2 and class 3
IPC Class 2 and IPC Class 3 are the two different categories of the printed circuit board. These classes help buyers find the best-printed circuit board that suits their needs. Below are the general differences between IPC class 2 and class 3:
-
Design rule
The design of IPC class 2 is too simple. It only focuses on achieving the desired function and specification via plating. At the same time, the component placement and layout design of IPC class 3 are all determined through a careful and strict process. The design of IPC class 3 aims to achieve high functionality and reliability.
-
Inspection
The inspection processes of both boards are also different. Inspecting IPC Class 2 includes visually examining defects like cracks or broken components. The inspector also does basic functional testing to ensure functionality.
The inspection of IPC class 3 is more detailed than IPC class 2 because it includes a detailed testing method. Microscopes and other tools are used to find defects that cannot be detected by the naked eye. It also includes tests like thermal cycling, vibration, and stress testing to ensure the board can handle extreme weather conditions.
-
Manufacturing constraint
The volume of IPC class 2 production is relatively higher because they are used in consumer electronics. Manufacturing costs and time are also lower as the minor defect is undetected. It also leads to higher yields. The high-end manufacturing needs are optional on this board.
The IPC class 3 is not mass-produced because the demand for these boards is only in the medical and automobile industries. Fabricator houses also take a lot of time and effort to produce these boards because it takes great effort to meet the exact requirements. Moreover, they are advanced boards that need high-end equipment.
Difference between IPC class 2 and 3 in assembly
We are sure that now you have understood that the high quality of the IPC class is class 3, and class 2 has lower quality than class 3. The following are the significant differences between IPC class 2 and 3-
-
Refined assembly
Class 3 boards are more reliable than class 2 boards. They also have a longer life expectancy. They are also appropriate for high-quality electronic devices. As a result, when compared to Class 2, their assembly cycle is reasonably refined.
-
Installation
The quality and thoroughness with which they will be examined is a significant difference between the two classes. The cleanliness and installation of parts of these class boards are extraordinary.
Class 3 products need deep cleaning because they are used in clinical and military products. Moreover, the careful installation of these boards is also necessary. In contrast, careful cleaning and installation are not necessary for class 2.
-
Barrel fill level
The total barrel fill manufacturers use in thru-hole leads is a significant difference between Class 2 and Class 3 boards. Class 2 boards utilize fewer barrels—even half—than class 3. In contrast, class 3 required three-quarter barrels. Getting the required amount of glue into a small, plated through-hole is delicate.
What is the difference between IPC class 2 and class 3 in manufacturing?
IPC class 2 and 3 also differentiate based on the manufacturing process. The manufacturing processes of both classes are also different. The following are the top significant requirements of Class 2 and 3 in manufacturing-
-
PCB through-hole plating prerequisite
Class 3 will be marginally astringent, particularly in the copper void. These boards are in circumstances where the copper plating in the opening barrel is absent. They will leave the penetrated-hole dielectric material uncovered.
IPC Class 2 allows a stipend of 5% for the critical opportunity of a single void in the board’s holes. In terms of plating thickness requirements, Class 3 requires one mil, while Class 2 requires 0.8 mils.
-
Annular ring and drill breakout
Drill breakout is another significant difference between classes 2 and 3. Class 2 boards allow breakouts to occur from the annual ring. In contrast, class 3 boards do not allow broken annular rings.
Class 3 boards must be tough because they indicate that there will not be colossal harm even after a breakout. When working with Class 2 objects, having a 90° break isn’t an issue as long as you keep minor dividing into the sidelong sides.
Conclusion
IPC class 2 and 3 are printed circuit boards that refer to the quality of this board. IPC Class 3 boards are considered top-quality boards. And the class 2 board is not as good as the class 3. We have tried to cover all the essential information about IPC class 2 vs. class 3 in this article.